Das ist weltweit einzigartig: In einer kleinen Tischlerei in Hamburg Eidelstedt kann man sein Kiteboard selber bauen. Angepasst an Größe, Gewicht und Vorlieben entstehen hier Unikate – verziert mit dem eigenen Design.
Es riecht nach frisch geschnittenem Holz. Durch die Fenster fällt milchiges Sonnenlicht, in den Strahlen tanzt der Staub, während Jannek Grocholl Löcher in das Holzbrett bohrt, das einmal ein Kiteboard werden soll. Geduldig fährt er mit seinen Fingerspitzen über die glatt geschliffene Oberfläche und zeigt so den Kursteilnehmern, wie sie die Löcher genau richtig platziert ausbohren können.
Kitesurfen
Zum Kiten braucht man Folgendes:
1. Den Kite, einen 9 bis 12 Quadratmeter großen Lenkdrachen, der für den Antrieb sorgt.
2. Die Bar ist mit dem Lenkrad eines Autos zu vergleichen, an ihr sind alle wichtigen Leinen befestigt, mit denen der Kite gesteuert wird.
3. Das Board, das viel kürzer und leichter als ein Surfbrett ist und auf den ersten Blick durch die Fuß-Bindungen an ein Snowboard erinnert.
4. Und schließlich noch den Wind – ohne den kann man den Wassersport nicht ausüben.
Die Stimmung in der Werkstatt ist gespannt, aufmerksam verfolgen die Teilnehmer Grocholls Erklärungen. Und dann geht es los: Zielstrebig verteilen sich die Teilnehmer an den Werkbänken, jeder vor seinem Board-Rohling. In diesem Wochenendkurs wollen die vier Männer zwischen 30 und 45 pünktlich zur startenden Saison ihr eigenes Kiteboard bauen. Die Kerne ihrer Boards wurden vorher von Grocholl vorbereitet – jeder ist anders und an die jeweiligen Wünsche angepasst.
Die Holzrohlinge sehen aus, als hätte man ein Surfbrett bis auf die unterste Schicht ausgezogen – ein nacktes Stück Holz in sportlicher Form liegt vor jedem Teilnehmer. Polonia, heißt die leichte Holzsorte, die dank ihrer langen Fasern besonders fest ist. Nach einem vorsichtigen Abtasten, zögerlichem Kennenlernen des Materials, beginnt der Bau. Was zuvor konzentriertes, stilles Zuhören war, wird zu geschäftigem Föhnen, Schleifen, Saugen und Bohren. Die Geräusche gehen wie in Wellen durch den Raum – nach jedem lauten Arbeitsschritt wird das Ergebnis betrachtet.
Im Sommer lieber surfen statt basteln
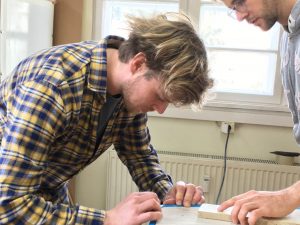
Grocholl hat wuscheliges Haar, so wie man es von einem Surfer erwartet. Gemeinsam mit seinem Kollegen Gerrit Hendricks zieht er von Werkbank zu Werkbank und hilft, wo es hakt. Die beiden haben das Board Lab vor gut einem Jahr gegründet. Einmal im Monat bieten sie hier einen Wochenendworkshop für maximal fünf Personen an.
Das erste Mal bewarben Sie ihren Kurs in einer Facebook-Gruppe. „Wir waren überrascht von der hohen Nachfrage und den positiven Reaktionen“, erzählt Grocholl. Die ersten Kurse waren sofort voll – im Sommer stagnierte die Nachfrage dann jedoch. „Kiter wollen in der warmen Saison lieber aufs Wasser als in die Werkstatt.“ Die Teilnehmer heute haben fast alle den Kurs von ihrer Familie zu Weihnachten geschenkt bekommen. Ein großzügiges Geschenk: 650 Euro kosten die zwei Tage, inklusive Board. Günstiger bekomme man ein neues Board aber auch selten, meint Grocholl.
Mit ihrem Lab stehen die beiden dem Markentrend in der Kitesurfing-Szene gegenüber. „Die Leute, die hier mitmachen, wollen so ein bisschen ausbrechen aus dem „Rumgepose“ und den Neonfarben“, meint Grocholl. Damit scheinen sie nicht allein zu sein: Online kann man in Video-Tutorials und Blogposts auf vielen Kanälen lernen, wie man ein Kiteboard selber baut. Aber einen Workshop, wie im Board Lab, gibt es bisher nur in Eidelstedt. “Vor Kurzem haben sich deswegen sogar Teilnehmer aus Australien angekündigt,” erzählt Grocholl.
„Ich hatte tierisch Bock auf dieses Handwerk“
Die Holzkerne sehen nach den ersten Stunden schon einen Rand angebracht und Löcher vorgebohrt. Jetzt sammelt sich die Gruppe im Vorraum der Werkstatt rund um einen massiven Holztisch. Beim gemeinsamen Mittagessen
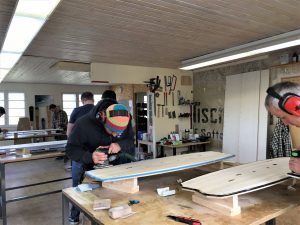
geht es um Kiten und um die Motivation von Grocholl und Hendricks. Die beiden können von den monatlichen Kursen nicht leben – das wollen sie aber auch gar nicht können: „Kiten und alles drum rum ist für uns nicht Arbeit, sondern Leidenschaft“, erklärt Hendricks. „Wenn wir hier 40 Stunden die Woche unter Erfolgsdruck arbeiten müssten, dann würden wir wahrscheinlich sehr schnell den Spaß daran verlieren“, ergänzt Grocholl.
Auf dem ersten von ihm selbst gebauten Kiteboard stand der heute 28-Jährige mit 14 – das Handwerk liegt irgendwie in der Familie. Sein Vater hat in seiner Jugend damals die ersten Snowboards Deutschlands gebaut. Grocholl lernte nach der Schule Bootsbauer und hat schon den ein oder anderen alten Kahn wieder fit gemacht, erzählt er stolz, „ich hatte tierisch Bock auf dieses Handwerk.“ In seiner Ausbildung lernte er professionell mit Holz und Kunststoffen umzugehen. Seitdem baut und verkauft er Bretter unter seinem eigenen Label Kantholz. Heute studiert er an der TU Hamburg Holz- und Kunststofftechnik, um mehr über die Wissenschaft hinter dem Handwerk zu lernen. Während er spricht, streicht er ein paar Holzspäne von seinem karierten, weichen Hemd. „Nach dem Studium will ich aber auf jeden Fall wieder in die Werkstatt.“
Zur “Hochzeit” eine Schicht aus Glasfaser
Zurück an die Werkbänke. Das große Ziel vor dem Ende des Tages ist die „Hochzeit“. Dabei wird der Holzkern in eine Schicht aus Glasfasern gehüllt – das verändert die Flexibilität und Festigkeit des Endprodukts. Mit einem geruchlosen Harz werden Brett und Glasfasern miteinander verklebt, über Nacht werden die einzelnen Schichten dann durch den Druck eines Vakuums zusammengepresst. Meist wird das Design des Boards auf einen dünnen Stoff
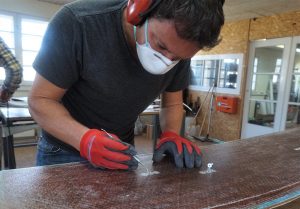
gedruckt und unter den Glasfasern angebracht, damit es besser geschützt ist. Die Teilnehmer schieben ihre Wunschmotive auf den Brettern hin und her und bestimmen die finale Position. Jeder arbeitet konzentriert: Es ist ein Marathon kleiner, wichtiger Arbeitsschritte, bis schließlich alle Boards auf speziellen Halterungen eingespannt sind und die Vakuumpumpe brummend beginnt, den Druck auf die Bretter aufzubauen. Um 21 Uhr ist der erste Tag vorbei, genau zwölf Stunden später stehen alle schon wieder kaffeeschlürfend in der Werkstatt.
Das große Kiteboard – Auspacken
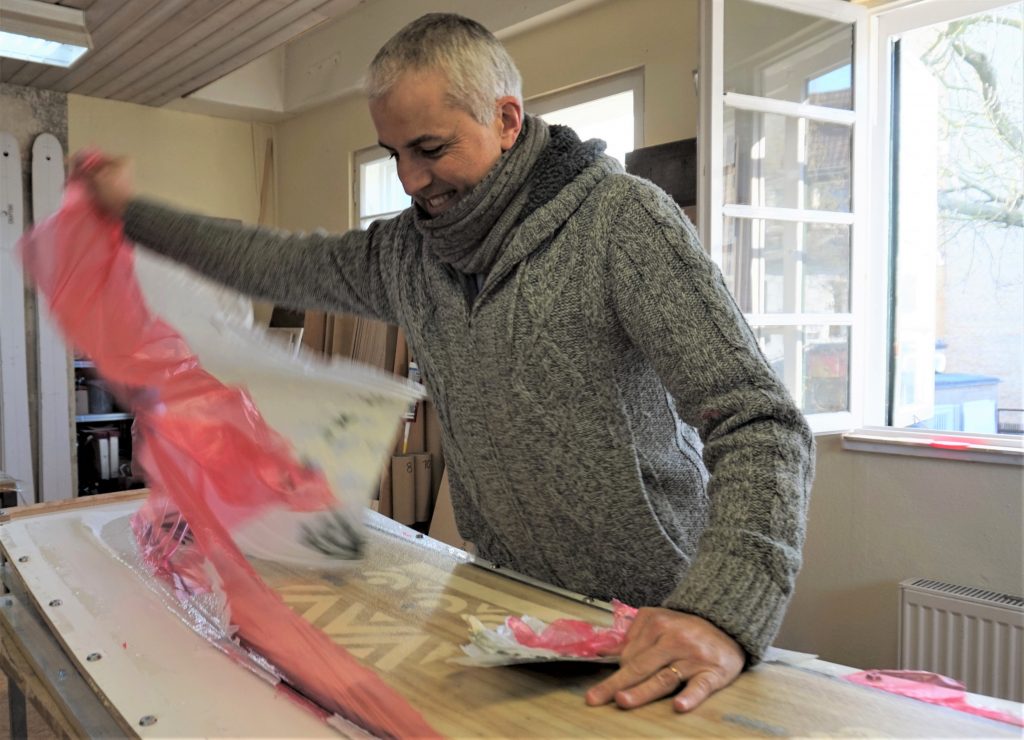
Die Kiteboards liegen wie aufgebahrt in der Werkstatt, alle nebeneinander, über Schläuche an die Pumpe angeschlossen. Zielstrebig lösen die Teilnehmer die Boards aus der Halterung und den äußeren Schichten. Eiliges Auspacken. Dann flutet Erleichterung den Raum. Ein stolzes Lächeln ziert das Gesicht von Grocholl und den einzelnen Teilnehmern.
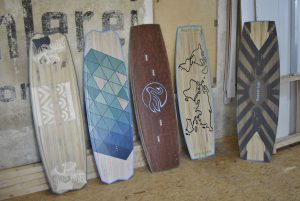
Alles hat gut geklappt, die Designs sind nicht verlaufen und gut erkennbar. Noch ist die Oberfläche der Bretter uneben, fühlt sich durch die Glasfasern an wie eine eingeschweißte Wolldecke. Sie müssen heute noch abgeschliffen und lackiert werden. Bis die Teilnehmer ihr Board zum ersten Mal testen können, müssen sie dem Lack mindestens einen Tag lang Zeit zum Trocknen geben. Danach wollen sie alle so schnell wie möglich aufs Wasser.
Hannah Lesch, Jahrgang 1994, überlebte bereits Wildwasser-Rafting mit Krokodilen in Namibia. Dort hat sie auch Bogenschießen gelernt. Nach dem Bachelor im Wissenschaftsjournalismus ging sie für ein Freiwilliges Soziales Jahr nach Afrika, um für die „Deutsche Welle Akademie“ Trainings für Medienschaffende anzubieten. Nebenbei organisierte sie ein Festival, bei dem in 48 Stunden Filme produziert wurden. Wissenschaftsjournalistin möchte sie werden, seit sie bei „Jugend forscht“ einen Preis gewonnen hat. Dafür kartierte sie Mauereidechsen. Und nein, mit Harald Lesch ist sie nicht verwandt. Ihren Namensvetter und ihr Idol würde sie trotzdem gerne mal treffen. Immerhin: Seine Gehaltsabrechnung wurde ihr beim Praktikum beim „Bayerischen Rundfunk“ aus Versehen zugestellt. Geöffnet hat sie diese aber nicht.
Kürzel: hl